汕头海湾隧道全长6680米,双向六车道,其中海底盾构施工段长3047米,分为东、西线两座隧道。
施工综合难度和风险首屈一指,中国工程院院士钱七虎、孙钧、周福霖等多次到现场调研了解相关情况,称汕头海湾隧道为“世界级挑战性工程”。
被称为“世界级挑战性工程”到底有多难?请了解下:
汕头海湾隧道具有“大、高、硬、浅、险”等特点。
“大”是指采用的泥水盾构机直径为15米级,属于超大直径;
“高”是指其处于高地震烈度区,达到8度;
“硬”是指岸上段孤石和海中基岩段,岩石的强度高;
“浅”是指盾构机上方覆盖层厚度薄,在始发地段隧道上覆土体仅为8.2米;
“险”是指海湾隧道处于软硬不均地层,地质复杂,施工难度大,安全风险高。
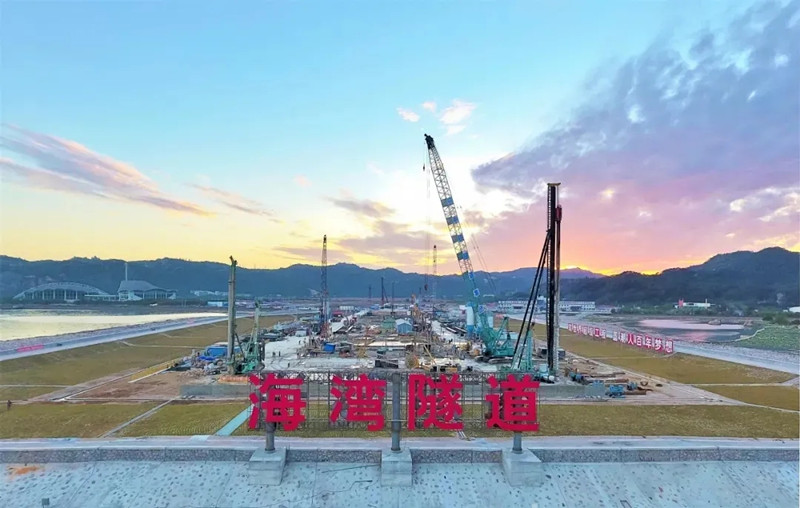
汕头海湾隧道的难,不仅难在已探知的五项挑战,更体现在层出不穷的未知挑战,无类似工程借鉴。
围绕汕头海湾隧道建设的种种争论贯穿了工程始终:建桥,还是建海底隧道?是盾构隧道,还是沉管隧道?是进口盾构还是国产盾构?……
特别是在盾构机选择上,无论是广东省交通厅、汕头市政府,还是建设单位中信集团,设计单位湖南省交通规划勘察设计院,施工单位中铁隧道局等,都承担了巨大的压力和风险。
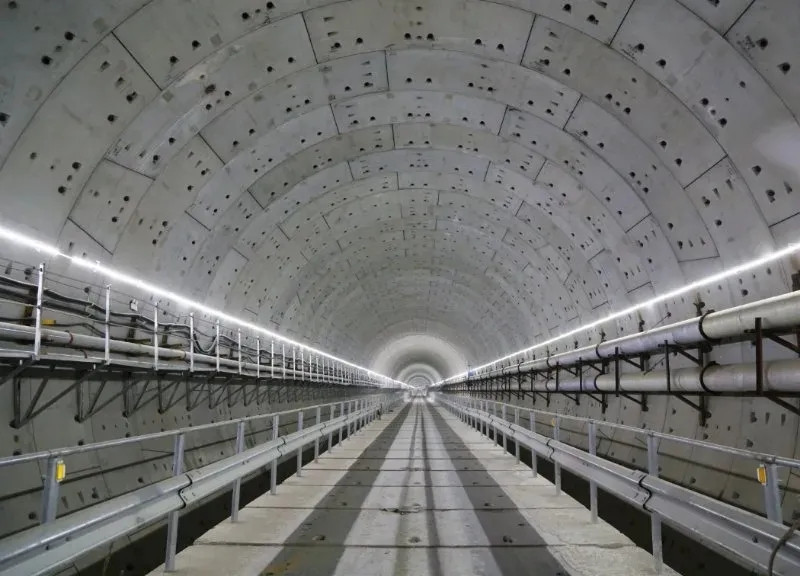
盾构机诞生于国外,以德国海瑞克公司为代表的当今国际著名盾构机制造商,具有丰富的制造业绩。我国虽然在21世纪初开启了盾构国产化进程,2008年,我国自主研制的首台复合式盾构机“中铁1号”在新乡下线,但此时的国产盾构应用范围有限,而国内制造15米级的超大直径盾构尚无先例。
一边是技术成熟的进口盾构,一边是正在成长需要在实践中汲取营养的国产盾构,面对汕头海湾隧道这样的“世界级挑战性工程”,选择进口盾构无疑能降低风险。
盾构机作为一种高端复杂设备,是“大国重器”代表之一,是一个国家科研水平、工业制造水平和综合国力的重要体现,国产盾构经过几十年的追赶,取得了飞跃的发展。但国产盾构仍有许多空白需要填补,其中一个重要原因就是,许多人都倾向于选择成熟的进口盾构,而不愿承担国产盾构应用过程中所带来的风险,以至于国产盾构错失了很多成长机会。
最终在总包方技术团队的坚持下,“一中一外”两台盾构同场竞技的方案被确认,国产盾构第一次迈进15米级超大直径领域。
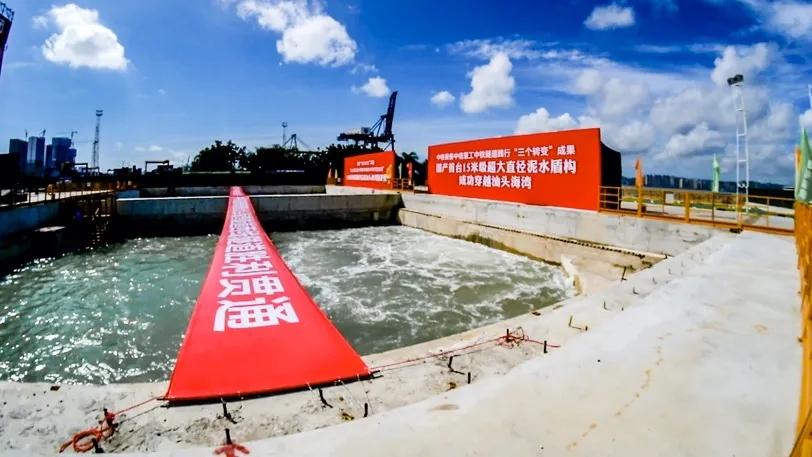
作为这台国产盾构制造商,中铁装备的副总经理王杜娟的心里别有一番感受:“国产盾构用几十年走过了发达国家近两百年的历程,汕头海湾隧道是时代赐予我们的舞台,我们要做的就是无愧于这个舞台、无愧于这个时代。”
2018年4月,进口盾构从汕头海湾隧道南岸始发,历时736天,穿越苏埃海湾,于2020年5月成功抵达北岸。
2018年10月,国产盾构亦从汕头海湾隧道南岸启航,历时660天,穿越苏埃海湾,于2020年8月成功抵达北岸。
国产盾构和进口盾构先后始发、同向掘进、同台竞技,在苏埃海湾20余米的水下,共同演奏了惊艳世界的壮美音符。
中国技术挺起中国制造的脊梁
自2018年10月始发以来,“中铁306号”在掘进过程中遭遇了诸多困难和挑战:盾构机上方覆盖层厚度薄,地质复杂,隧道处于软硬不均地层,给设备带来了严峻的考验。
特别突出的是,西线隧道第三段基岩凸起长度达71.8米,岩石主要为中微风化花岗岩,地勘揭露岩石最高强度达216兆帕,是东、西线盾构隧道六段基岩凸起中岩石强度最大、施工风险最高的一段。
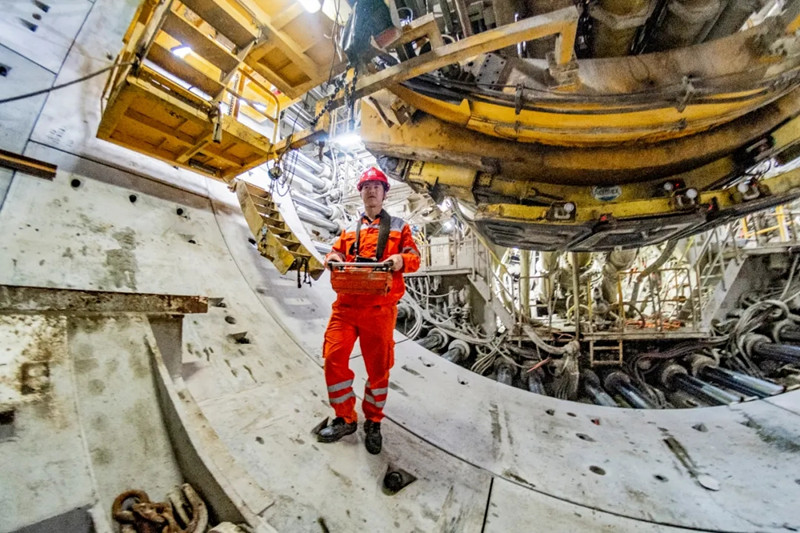
为更有效应对超强硬岩,中铁装备现场技术服务团队积极协助施工单位,根据西线基岩掘进实际情况,最终通过试验模拟、针对性装置和信息化管理,精准地控制掘进参数,优化了刀具配置,成功克服了地质带来的各项施工难题,确保了设备顺利推进。掘进期间创下最高月进尺460米,日进尺25米,周进尺150米的好成绩,不仅刷新了国产超大直径泥水平衡盾构机的施工掘进纪录,也创造了汕头海湾隧道全线隧道的月掘进纪录。
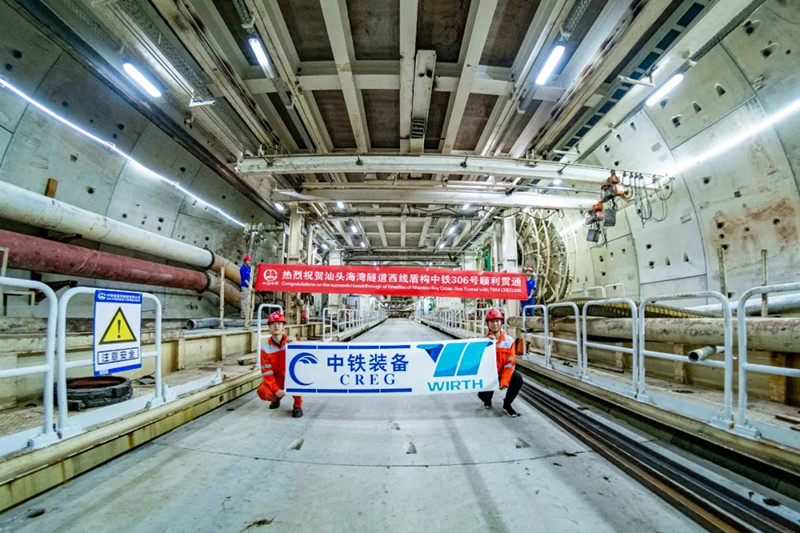
“中铁306号”在孤石、基岩、8度地震烈度区等复杂施工条件下,历时651天,成功绘出一道长达3047米的海底长虹,创造了国产高技术装备铸造超级工程的新纪录,也掀开了我国跨江越海隧道建设新篇章,对未来中国及世界海峡隧道建设具有重要的指导意义。
中国工程院院士周福霖评价:“汕头海湾隧道建设中形成的高烈度地区隧道建造体系,对未来中国隧道建设、世界隧道建设将起到一个示范作用,对我国未来开工建设的琼州海峡隧道、渤海海峡隧道、台湾海峡隧道等具有重要的指导意义。”
