从珠海平沙的红树林湿地公园眺望,黄茅海跨海通道犹如长龙卧波,5座“小蛮腰”出海,气势非凡!
12月11日,中铁宝桥参建的国家级重点工程,黄茅海跨海通道正式通车,为粤港澳大湾区跨江跨海交通网络再添“关键一横”。这是继6月深中通道开通后,粤港澳大湾区跨海跨江通道群,年内迎来的又一重磅成员。
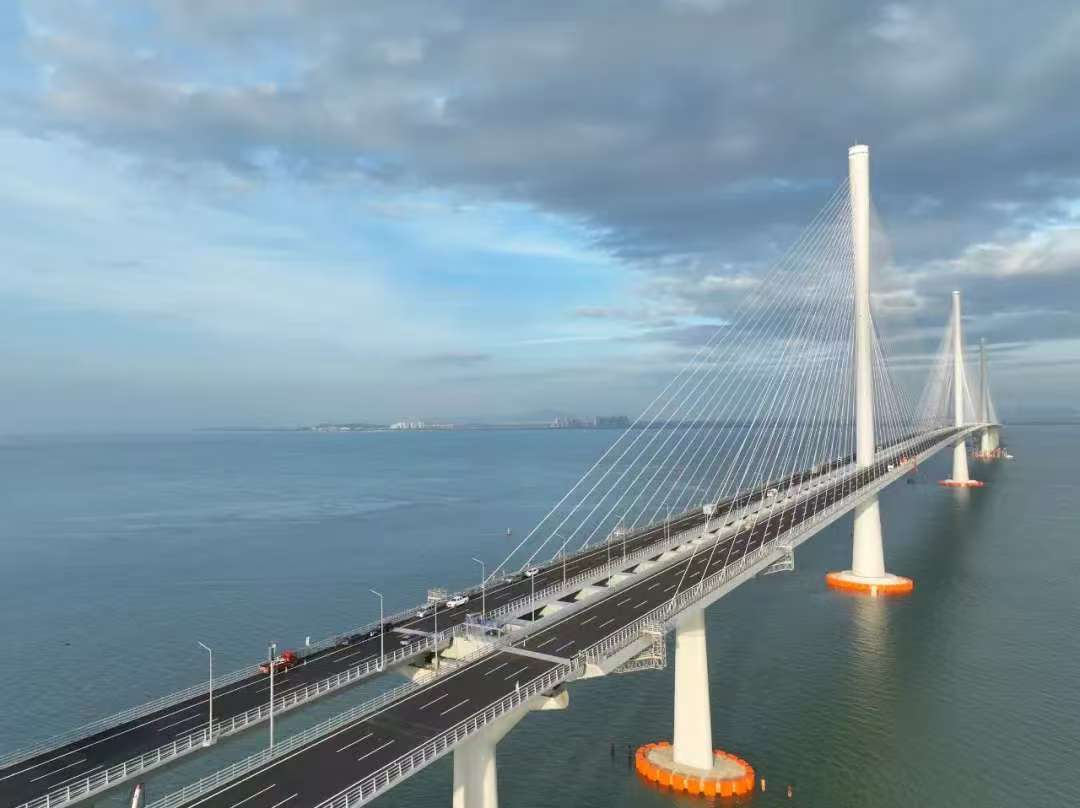
黄茅海跨海通道项目东连港珠澳大桥,西接西部沿海高速,是组成粤港澳大湾区的重要跨江通道。项目全长约 31km,海上段长度约14km,设计时速100km/h。其中,中铁宝桥承制了该项目G3标段黄茅海大桥主桥钢箱梁与主塔钢锚梁的生产制造任务。
黄茅海大桥主桥为大断面分体式钢箱梁结构,钢箱梁全长2200m,是黄茅海跨海通道项目控制性工程、世界最大三塔公路斜拉桥。
创新领航 智能建造
建设过程中,因大桥跨径大、载荷能力要求高,桥面板为U肋正交异性桥面板,对钢箱梁制造的匹配精度要求极为严格。技术团队依托中铁宝桥舟山钢桥梁基地,构建了国内先进的钢桥梁智能制造“五线一系统”,涵盖板材智能下料切割生产线、板单元智能焊接生产线、节段智能总拼生产线、钢箱梁智能涂装生产线、钢护栏智能制造生产线以及车间制造执行智能管控系统,实现了钢桥梁制造自动化、数字化、智能化、绿色化,单元件制造智能设备使用率达100%,生产效率提高了40%以上。

▲板单元智能焊接生产线
在焊接工序方面,自主研发的 U 肋内外专机焊接智能控制系统,可实时监测焊接电流、电压、焊接速度等参数,并基于大数据分析进行自适应调整,成功解决了焊接质量不稳定、易出现缺陷的问题。
创新突破 技术攻坚
针对黄茅海大桥钢箱梁制造关键环节,技术团队积极进行攻坚,通过研发了大断面分体式钢箱梁结构一次整体组拼及微变形无应力控制技术、基于协作式焊接机器人的分体式钢箱梁全场景自动化焊接及全过程无码制造技术,实现了分体钢箱梁几何尺寸与变形的有效控制和高精度制造,大幅提升了钢箱梁整体质量与耐久性。
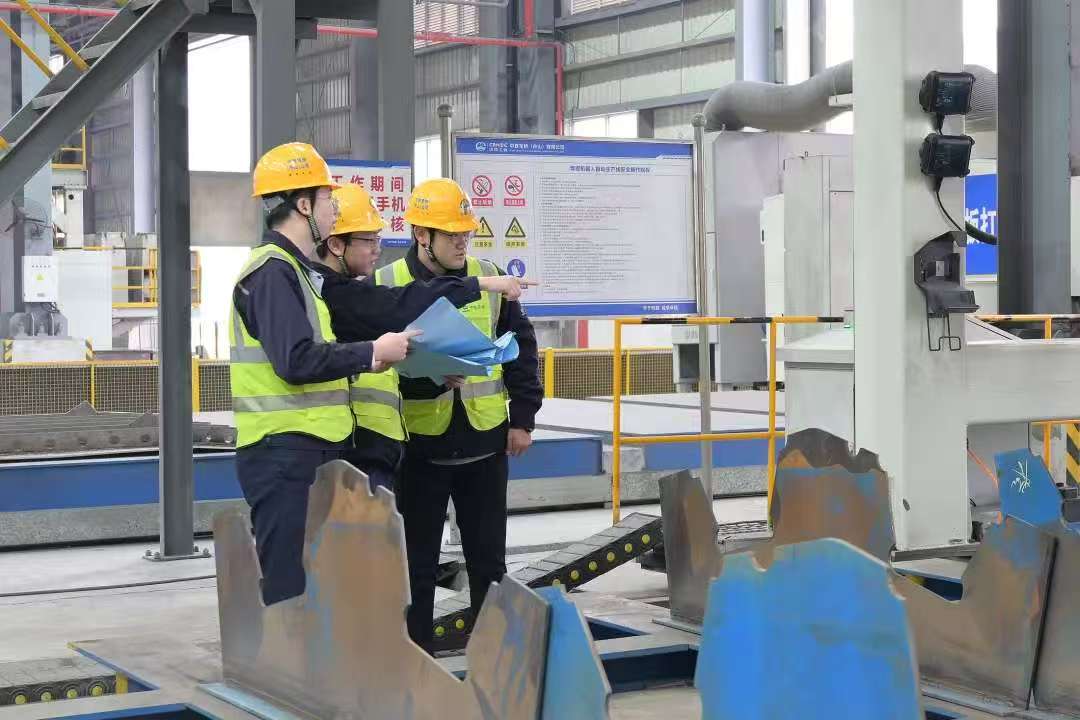
同时,创新加劲机器人定位组装技术,运用多传感器融合定位算法,攻克了加劲部件定位不准、效率低下等难题,实现加劲部件的快速精准定位,定位误差较传统工艺降低80%以上,有效提高组装效率与质量稳定性。
创新驱动 品质保障
项目建设以来,技术团队秉承工匠精神,精心组织、科学规划,通过施工管理流程和项目规范化建设,搭建项目信息管理平台,实现工作进度实时监控、高效协调;建立了完善的质量监督体系,实行质量责任追溯制度确保质量目标始终如一;积极探索新的施工工艺和技术,大幅提升焊接质量和工作效率。
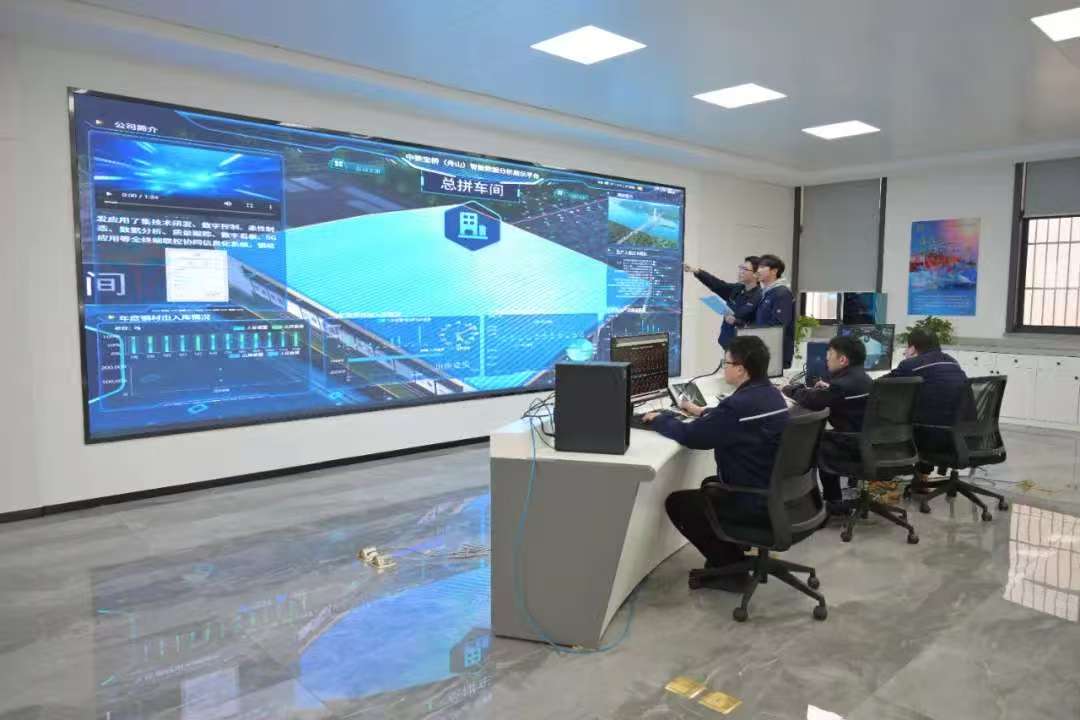
▲项目信息管理平台
中铁宝桥依托黄茅海大桥项目累计荣获中国公路学会全国公路微创新大赛银奖1 项,铜奖 2 项,并成功申报发明专利 7项,1项已经授权,同时在中文核心期刊上发表论文4篇。
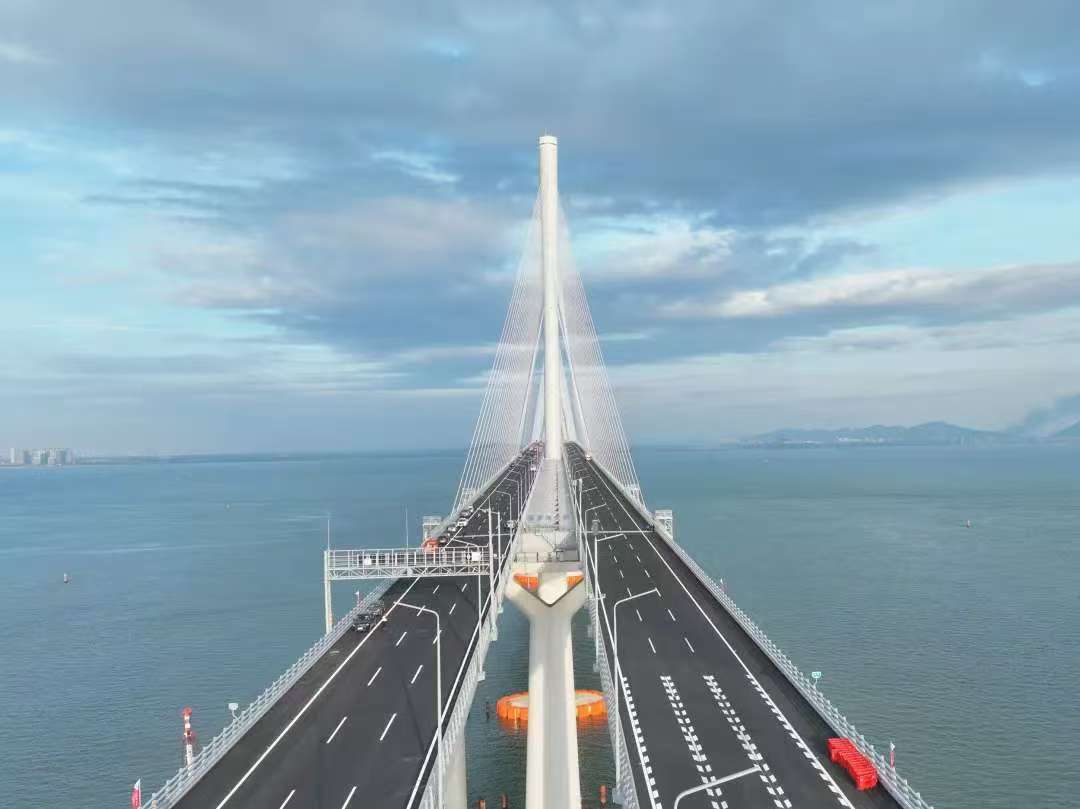
如今,黄茅海跨海通正式通车。珠海到江门的通行时间从1个多小时缩短至30分钟左右,进一步促进粤港澳大湾区人流、物流、资金流、信息流的加速融合,为区域经济发展注入澎湃动力。