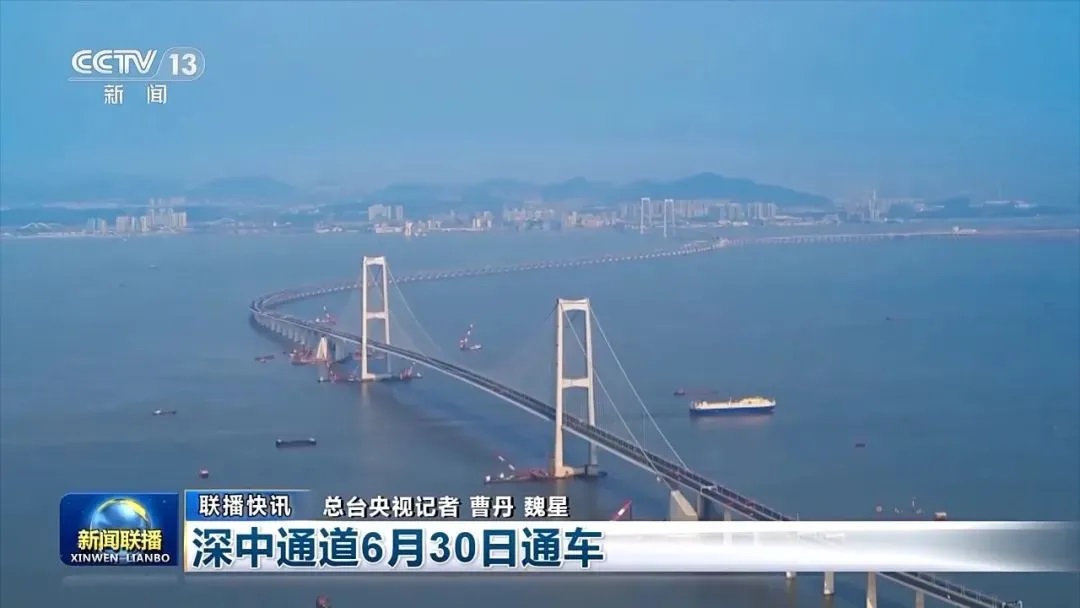
6月30日,历时7年建设的深中通道项目正式建成通车。东起深圳,西至中山,全长24公里,30分钟内即可通达。
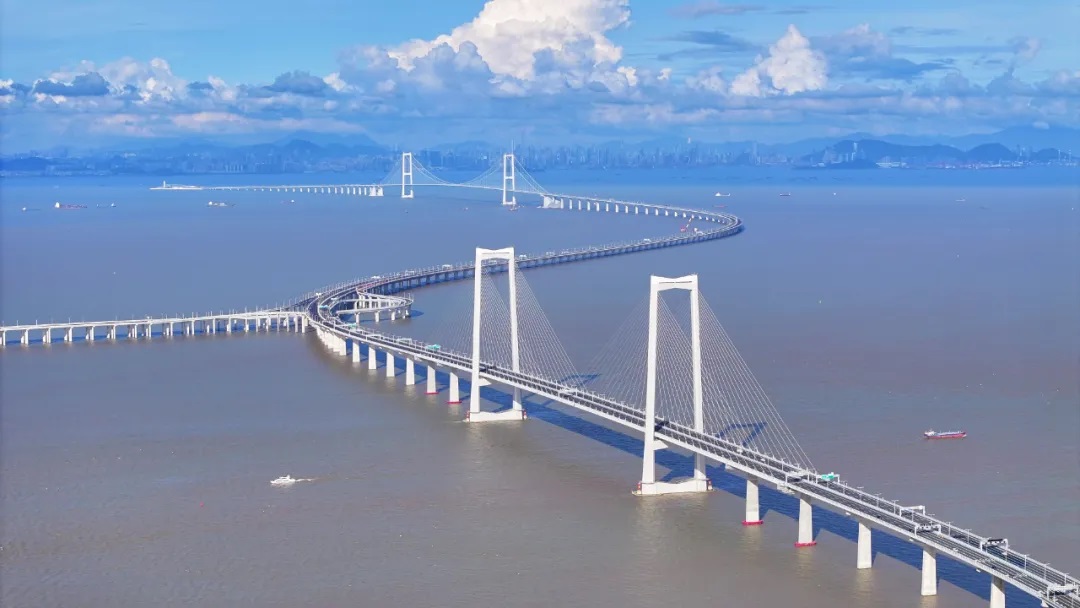
深中通道项目全长约24.03公里,是集“桥、岛、隧、地下互通”为一体的世界最大跨海集群工程。
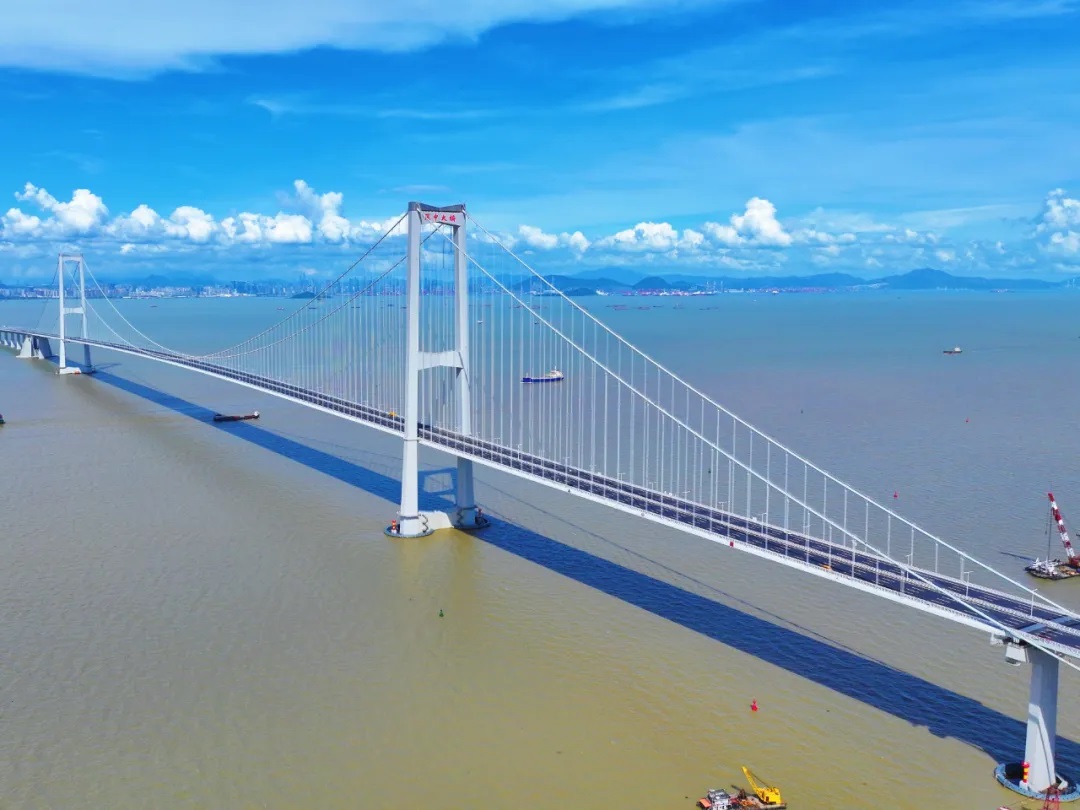
中铁工业旗下中铁山桥、中铁宝桥承制了该项目G05合同段和G04合同段钢箱梁制造任务,包括深中大桥(原名伶仃洋大桥)、中山大桥、横门泄洪区非通航孔桥、西泄洪区非通航孔桥、浅滩区非通航孔桥、万顷沙互通匝道桥及附属设施,全长7.24公里,钢结构总重约18.3万吨,以世纪工程献礼建党103周年。
探索,走在前列!
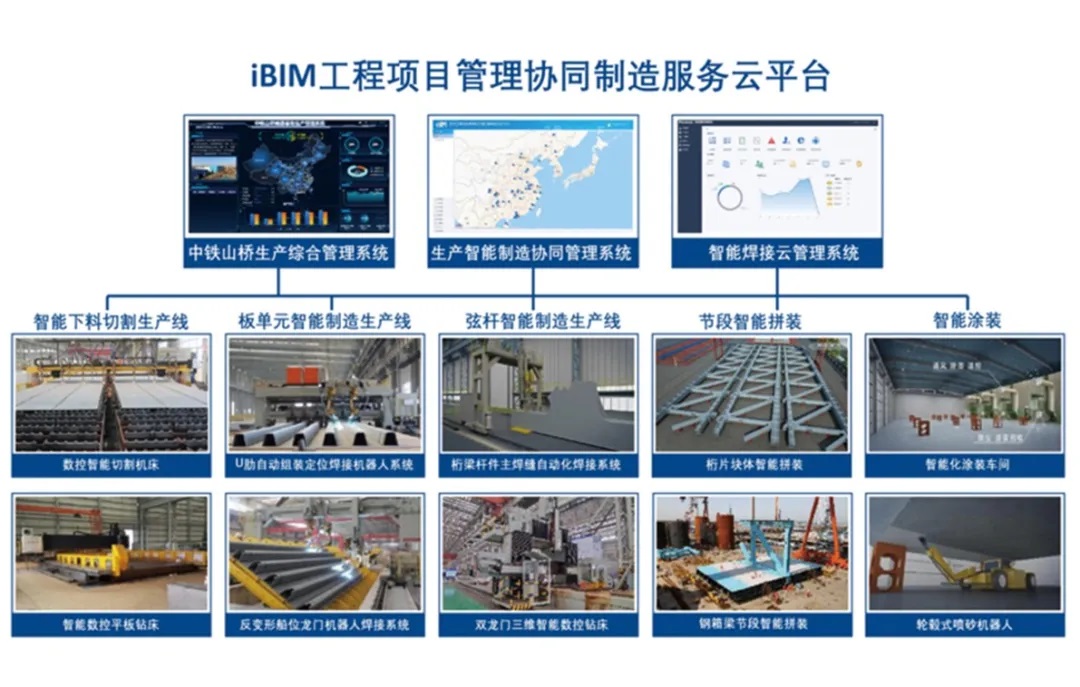
中铁山桥构建了以车间制造执行智能管控系统(iBIM)为核心,企业资源计划(ERP)、信息化焊接管理系统(iWeld)、数控设备数据采集系统(DNC)等系统信息集成的管理系统,通过基于BIM技术的钢箱梁智能设计,实现BIM制造模型信息管理、BIM制造模型工艺设计信息自动抽取、BIM设计模型轻量化、工艺设计3D仿真、产品数据管理等功能,全面提升钢箱梁建造质量和综合管理水平。
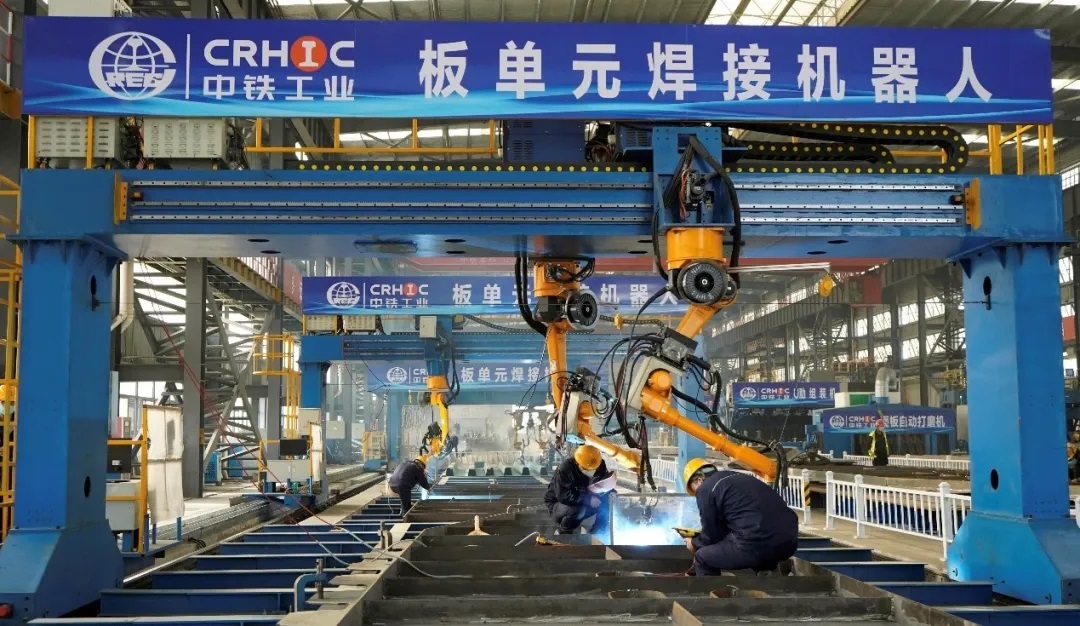
中铁宝桥研究并应用“跨海集群工程桥隧钢结构智能制造关键技术”,以智能制造信息化建设项目暨“一中心、三示范”规划为抓手,打造了以板材智能下料切割生产线、板单元智能焊接生产线、节段智能总拼生产线、钢箱梁智能涂装生产线以及车间制造执行智能管控系统为核心的“四线一系统”智能设备集群,使板单元制造智能设备使用率达到100%,生产效率提高30%以上,智能喷砂效率相比于传统手工喷砂效率提升5倍,全面提升钢箱梁制造的自动化、数字化、网络化、智能化水平。
攻坚,迎难而上!
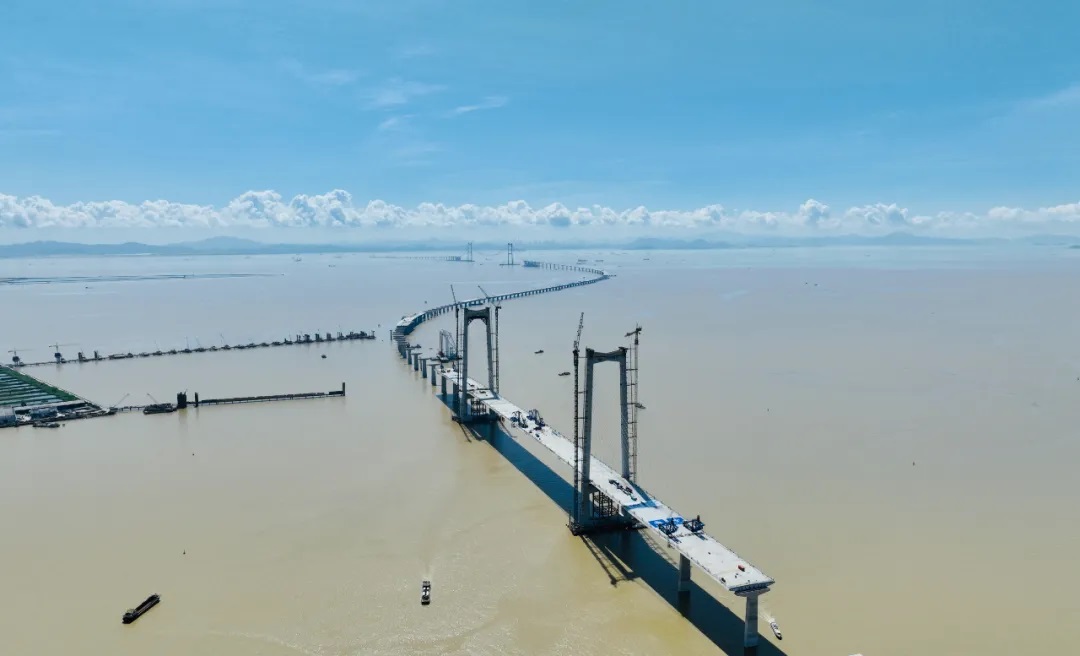
该项目钢箱梁种类多、结构复杂、制造难度大,围绕解决钢箱梁正交异性桥面板疲劳损伤等行业共性难题为突破点,中铁山桥自主研发了一系列新工艺、新装备,使生产效率提高了30%以上,焊缝质量稳定,平均一次探伤合格率99.9%以上,顶板U肋全熔透焊缝探伤一次合格率大于98%(超出项目预定指标2个百分点)。为解决部分浅滩区非通航孔桥大节段需要分幅制造或者开槽架设的难题,项目团队迎难而上创新研制了钢箱梁大节段出海平台方案,拓宽了港池运输大节段的方式。自2020年6月20日开始板单元制造,相继克服台风、暴雨等诸多不利因素,高质量完成了135片钢箱梁节段制造、发运和桥位连接任务,更是创造了29天完成整轮钢箱梁拼装的纪录。
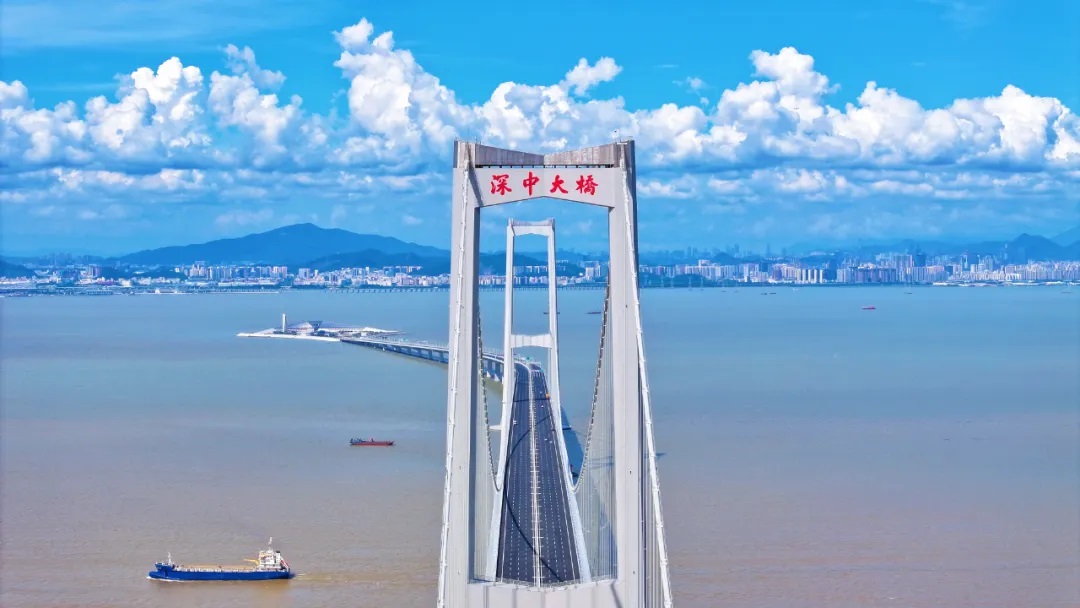
深中大桥为全离岸海中悬索桥,连接梁段之间的临时匹配件仅提供较弱的刚度,不利于抗击台风。为在台风来临之前完成全部焊接工作,中铁宝桥项目团队在钢箱梁吊装过程中使用吊焊结合的新技术,通过临时拉杆施加张力或撑力调整相邻两片梁的夹角,使其满足二期恒载加载前的线形,从而实现吊装期间两片梁进行焊接的可能。深中大桥吊装工作于2023年1月12日开始,同年4月28日实现全桥合龙,5月28日完成全桥环缝所有焊接工作,再次刷新了悬索桥环缝施工新纪录。
创新,成果斐然!
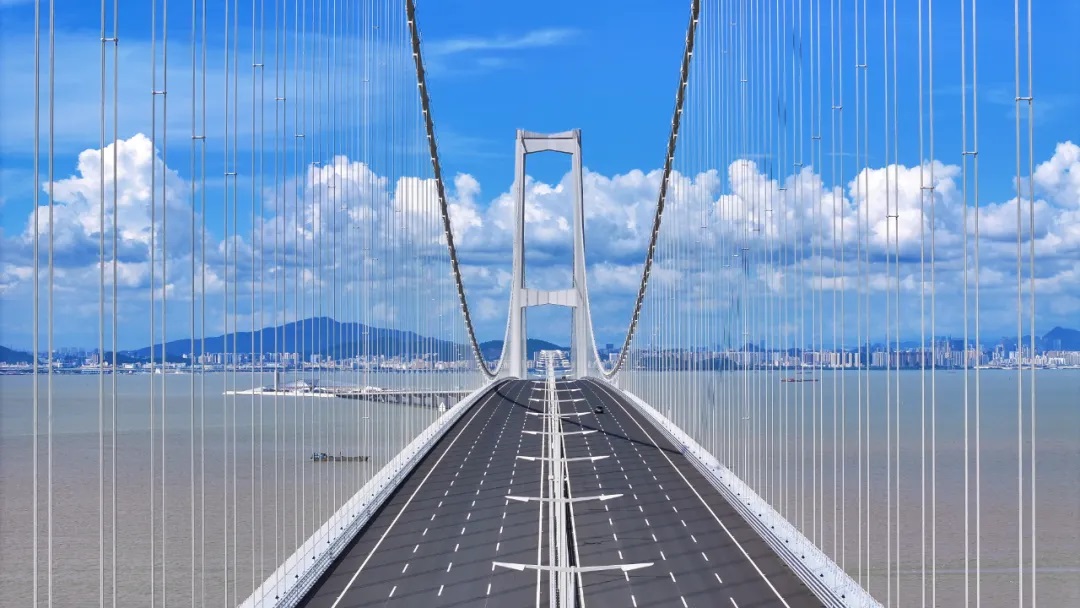
在项目生产制造过程中,中铁工业累计申报专利32项,实用新型19项,在专业期刊发表学术论文11篇,参编专著2本,编制团体标准2部,申报工法2个。在第十三届太平洋钢结构会议暨2023中国钢结构大会中,中铁山桥、中铁宝桥项目团队申报的《跨海集群工程桥隧钢结构智能制造关键技术研究及应用》项目获“2023年度中国钢结构协会科学技术奖特等奖”。
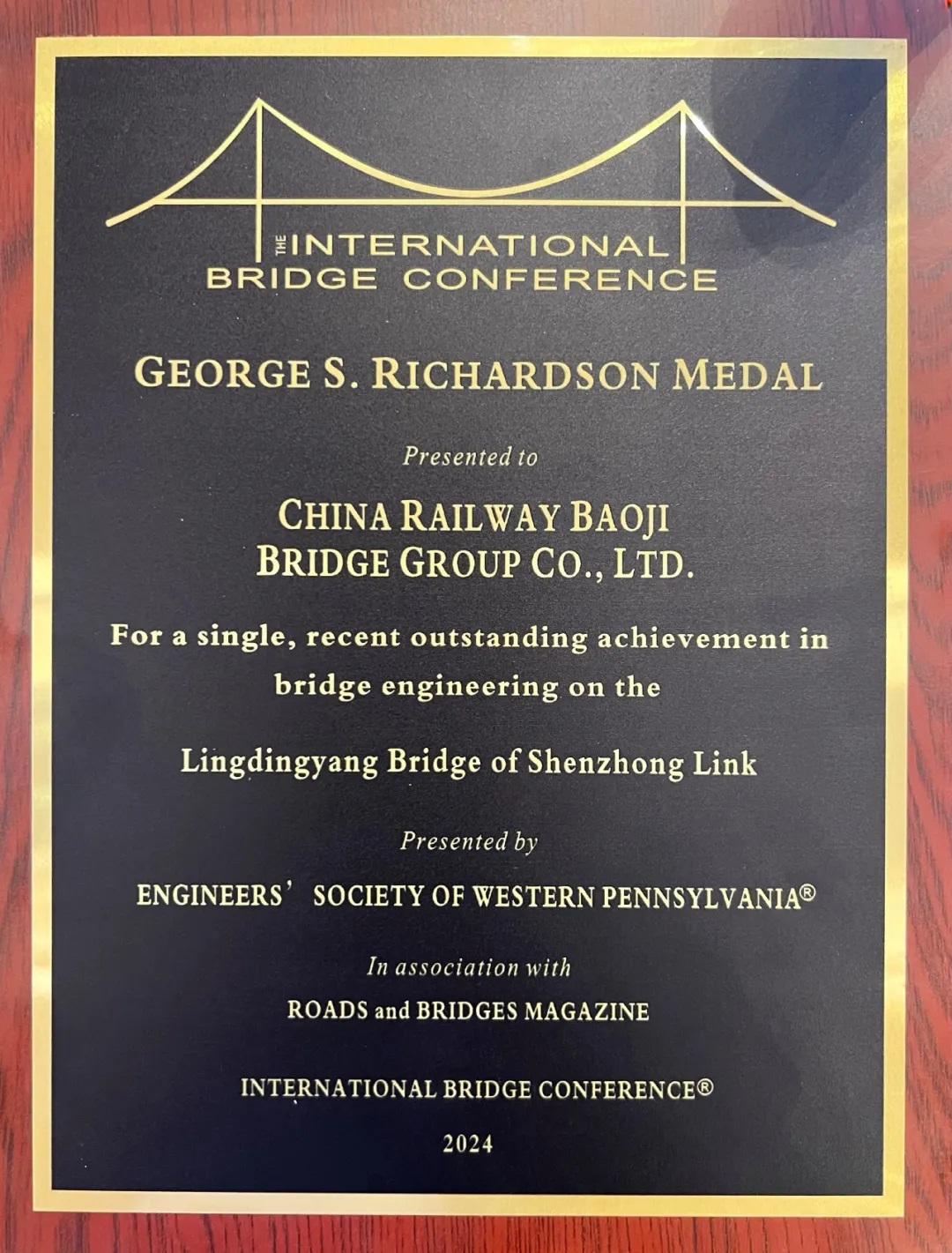
与此同时,中铁山桥深中通道项目部荣获“广东省工人先锋号”,中铁宝桥参建的深中大桥捧回国际大奖——“乔治·理查德森奖”,成为本届中国唯一一个获此殊荣的桥梁工程项目,同时也是奖项设置以来中国第十个获此殊荣的项目。